Onshore
Conquering Onshore Energy Frontiers
For decades, McDermott has dominated the onshore energy arena, leaving an indelible mark on oil and gas field development, processing, and storage terminals. We're not just industry players; we're trailblazers reshaping the onshore landscape.
Services are provided from concept to completion through our turnkey EPFC solutions:
- LNG solutions
- Refining and petrochemical facilities
- Gas processing plants
- Oil and gas import and export terminals
Fully integrated EPFC execution with strategically located global fabrication facilities
Complete project lifecycle expertise, from feasibility through to commissioning, start up and initial operations
World leader in modularization
years experience
operating e-drive LNG facility
net-zero LNG facility
With strategically located execution offices and fabrication yards in the Americas, Middle East, and Asia, McDermott optimizes execution based on project priorities. As a global, integrated EPFC contractor, we complete over 29 million work hours of capacity and ~300,000 metric tonnes of fabrication yard throughput annually.
The capacity and capabilities of each fabrication yard provide the flexibility to fabricate and assemble a full range of solutions for different project types, from 20,000 metric tonne HVDC platforms, in excess of 12,000 metric tonne complex process modules, 5,000 metric tonne PAR modules to container-sized truckable modules. We deliver our projects using consistent tools, systems, and standards to deliver superior results safely, even in the most challenging environments.
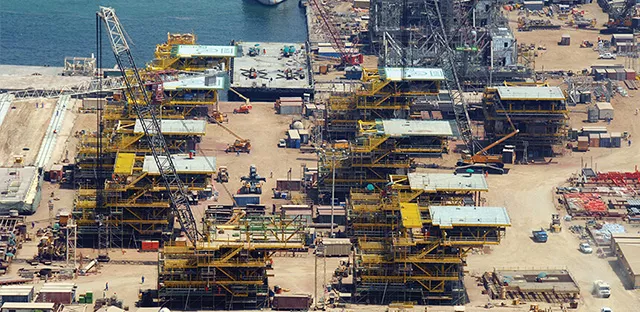
Flexible modular design
Modular execution planning
Strategically located global fabrication yards
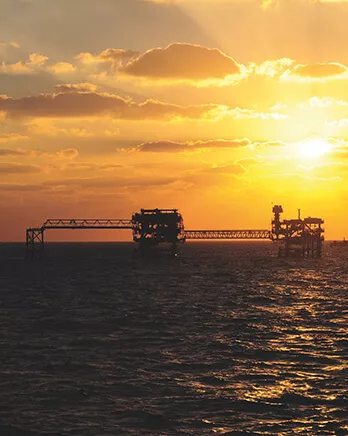
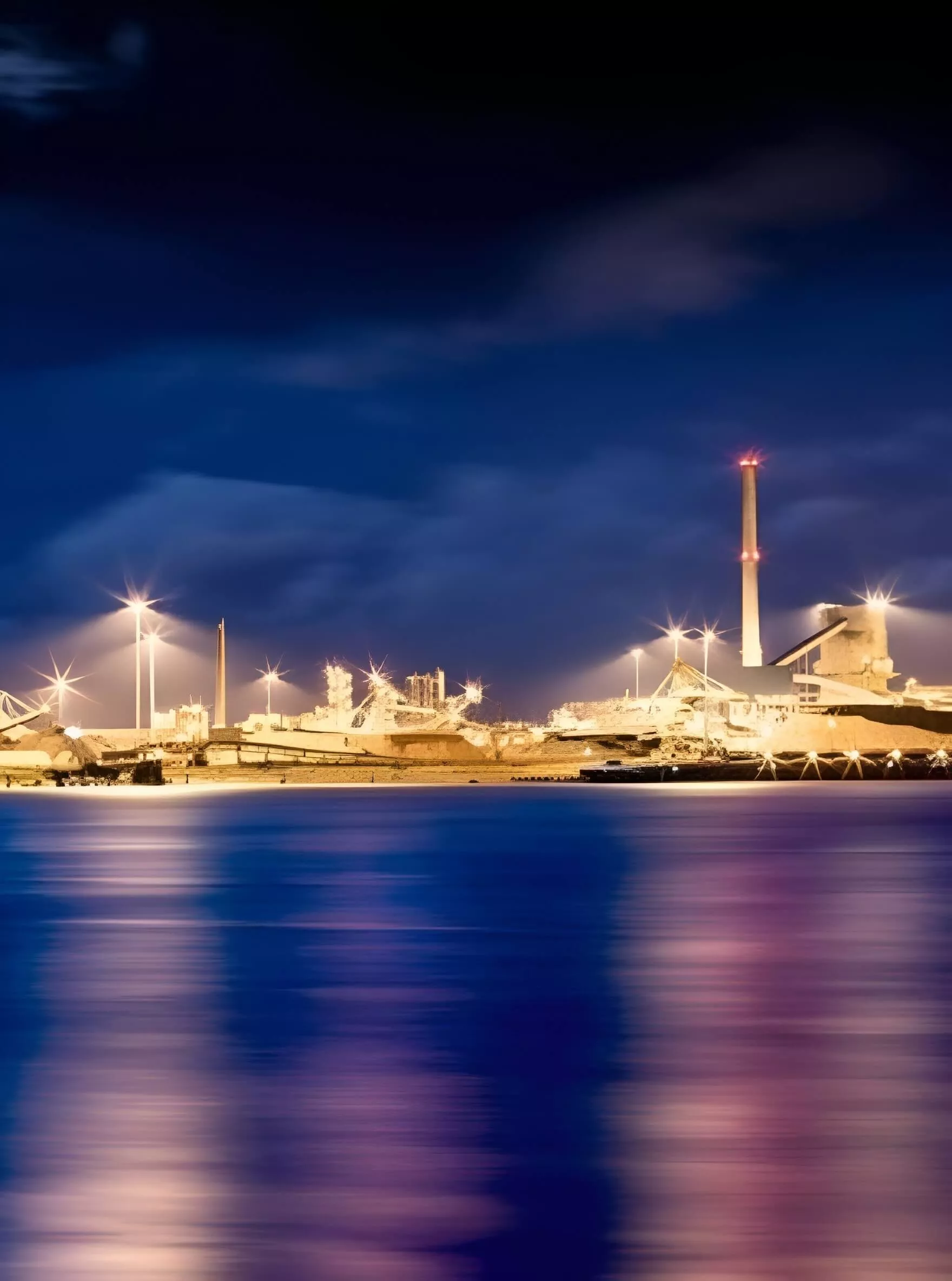
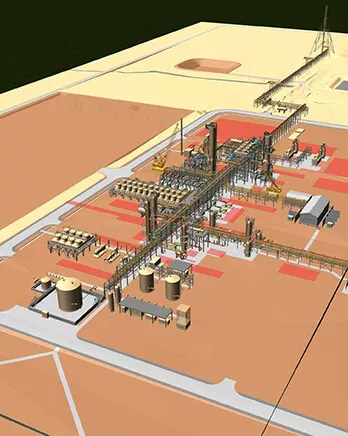
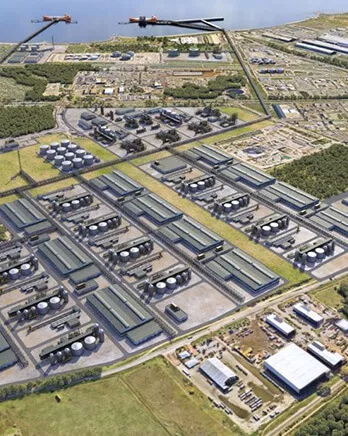

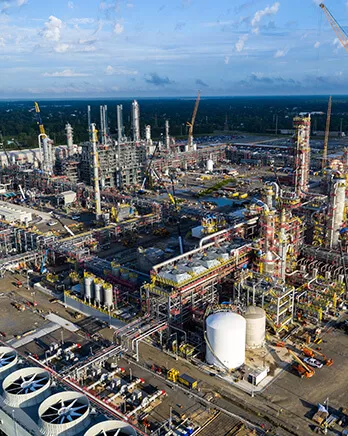
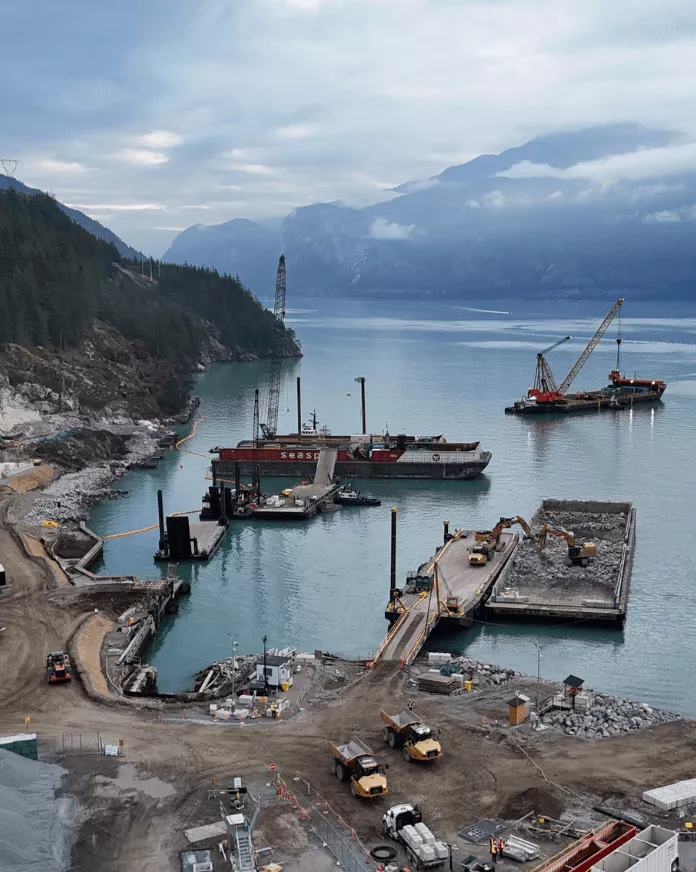
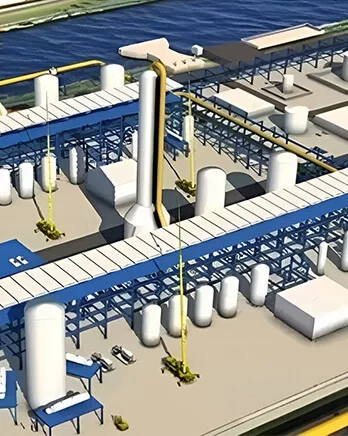
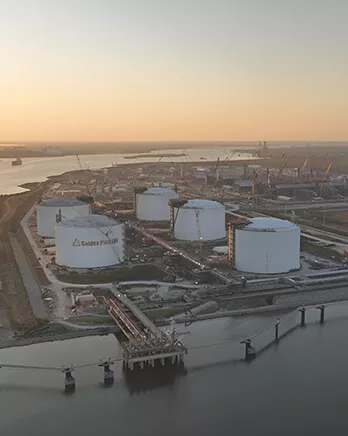
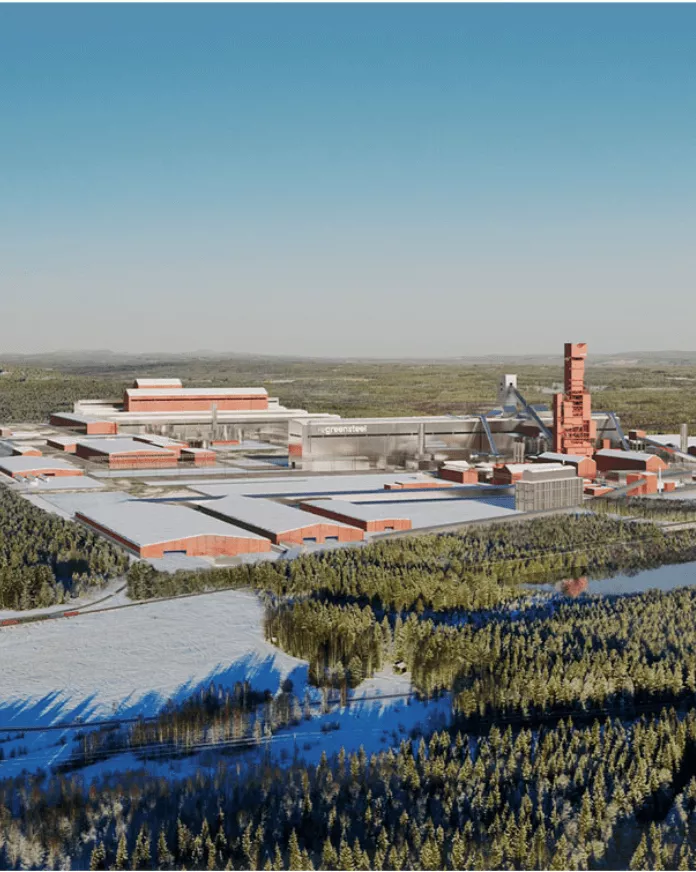
End-to-end delivery from capture to sequestration. McDermott has long experience in CO2 capture, utilization, and storage applications. Our collaborations with CCUS technology providers help customers reach their decarbonization goals.
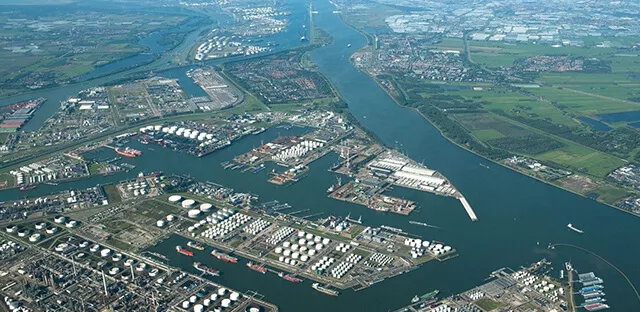
Full value chain integration
Fit-for-purpose technology selection and optimization
Standard modular CO2 dehydration and compression solutions to enhance project viability and execution
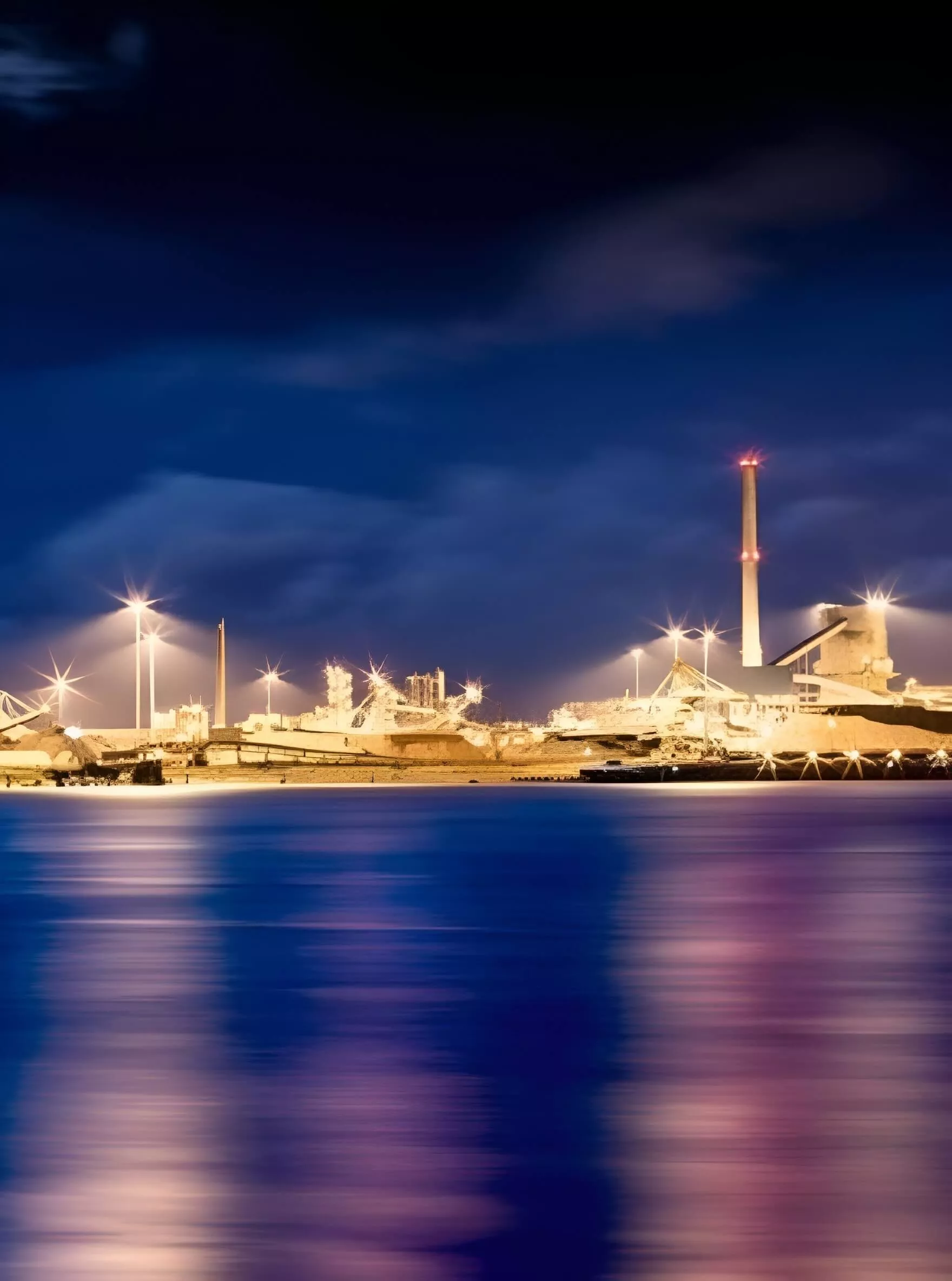
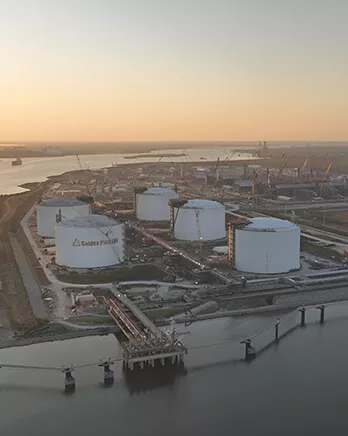
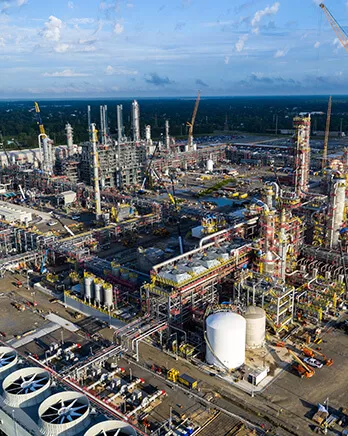
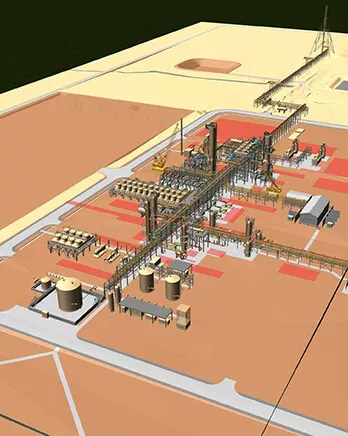
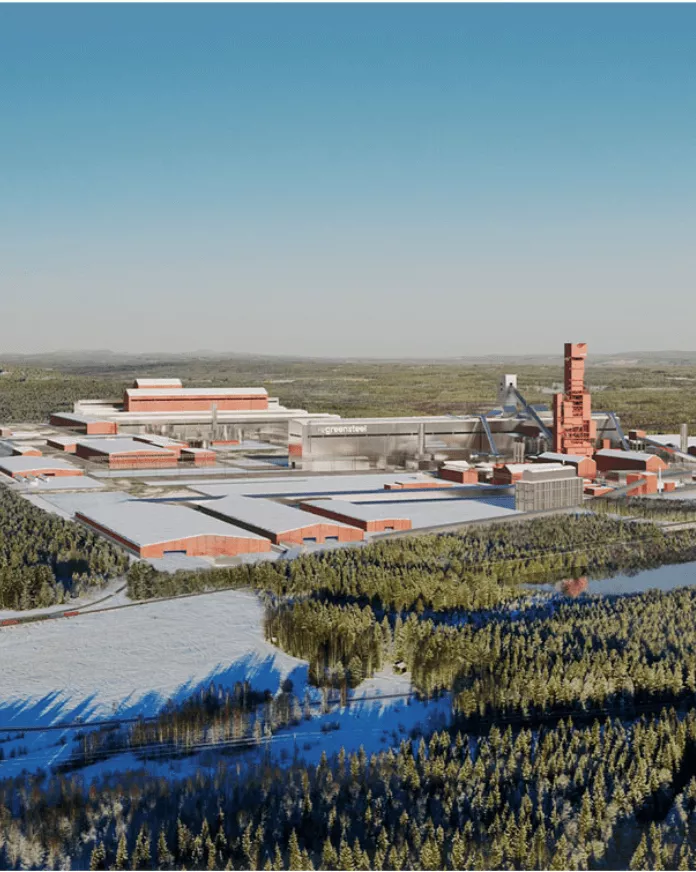
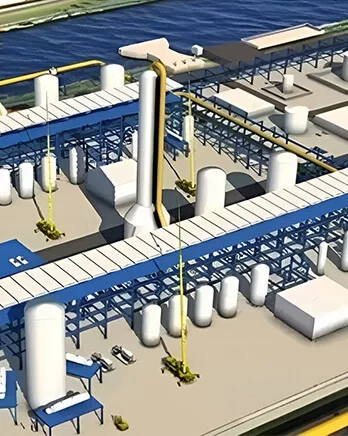
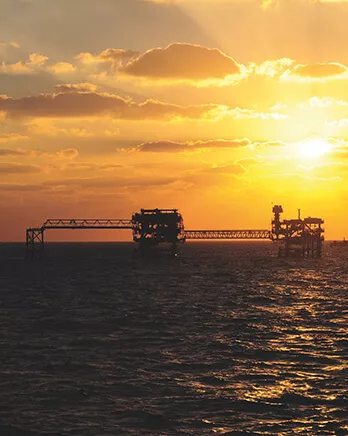
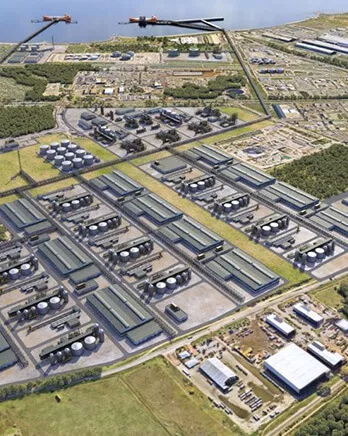
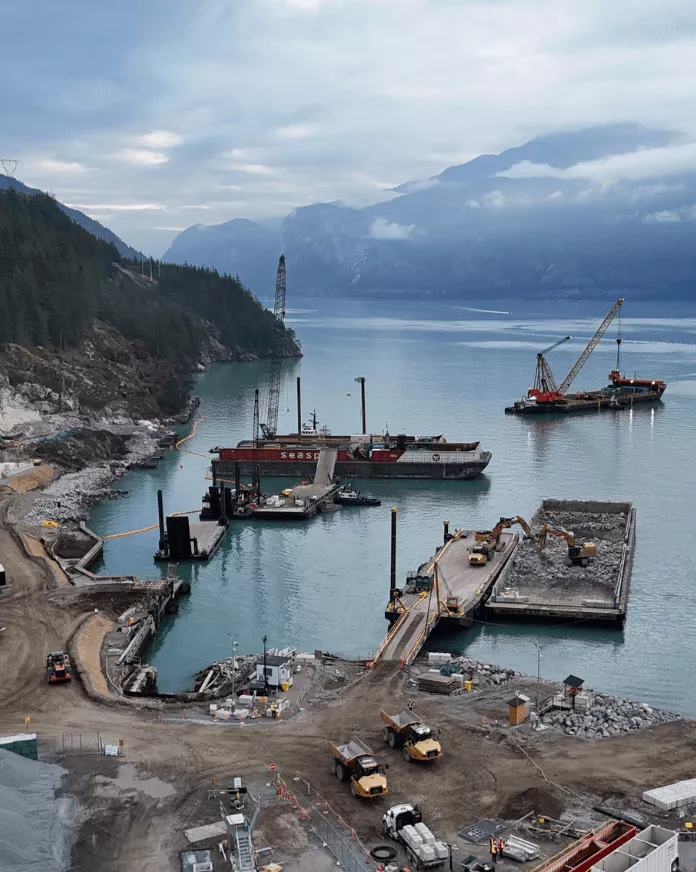

Through our in-house expertise and capabilities, relationships with the industry’s top technology providers, we tap into a broad technology portfolio—including gas conditioning and treating, integration with LNG liquefaction, fractionation, deep ethane extraction and LPG recovery, and liquid product treating—to offer solutions across the natural gas value chain.
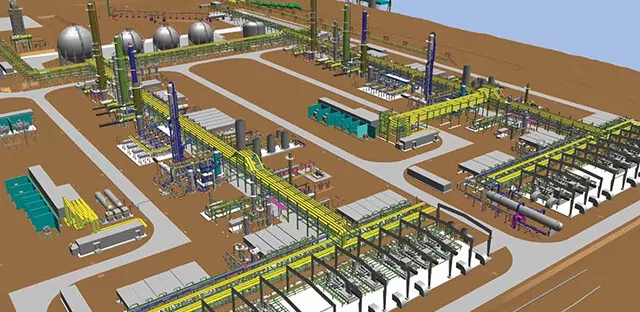
50 years of experience
300+ gas processing plants
26 BSCFD of gas processing capacity
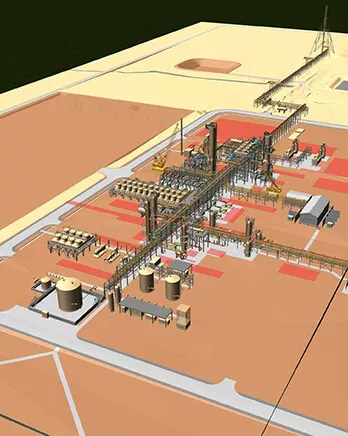
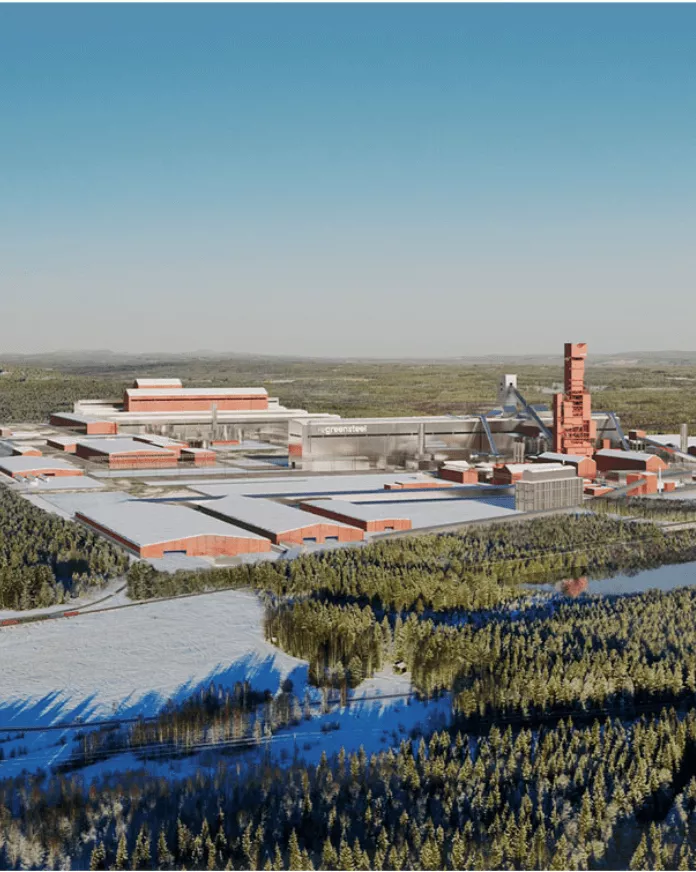
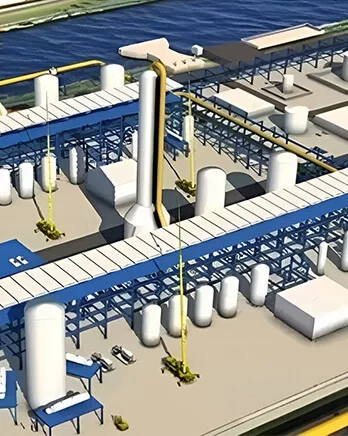
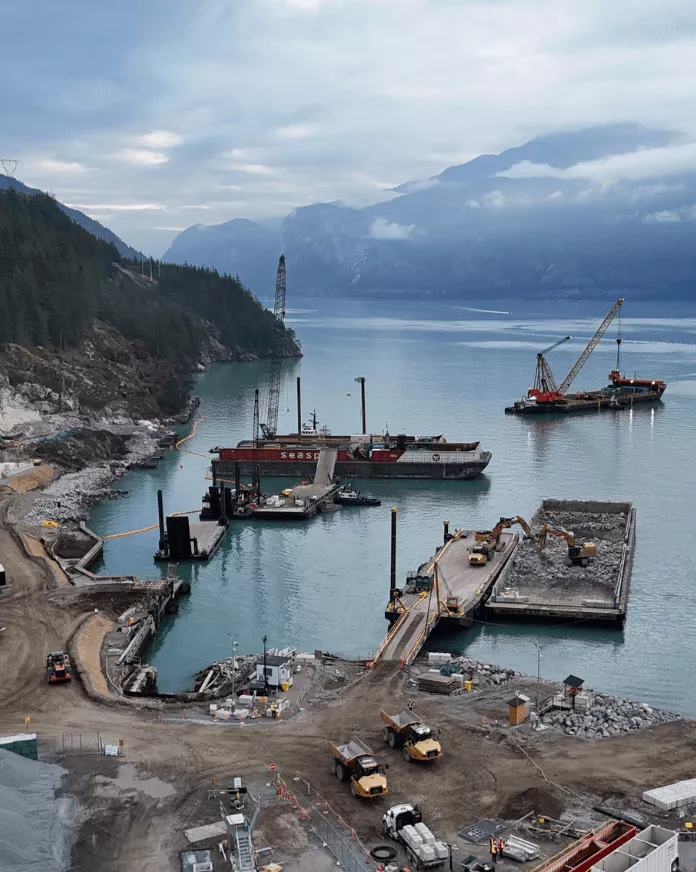
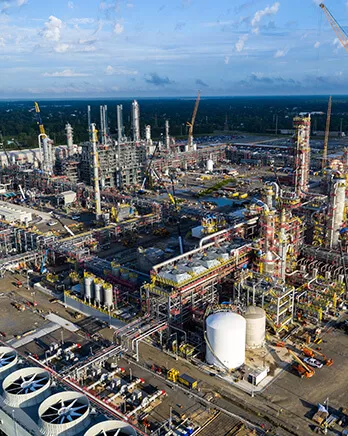
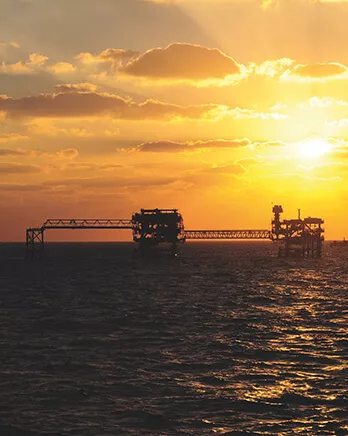
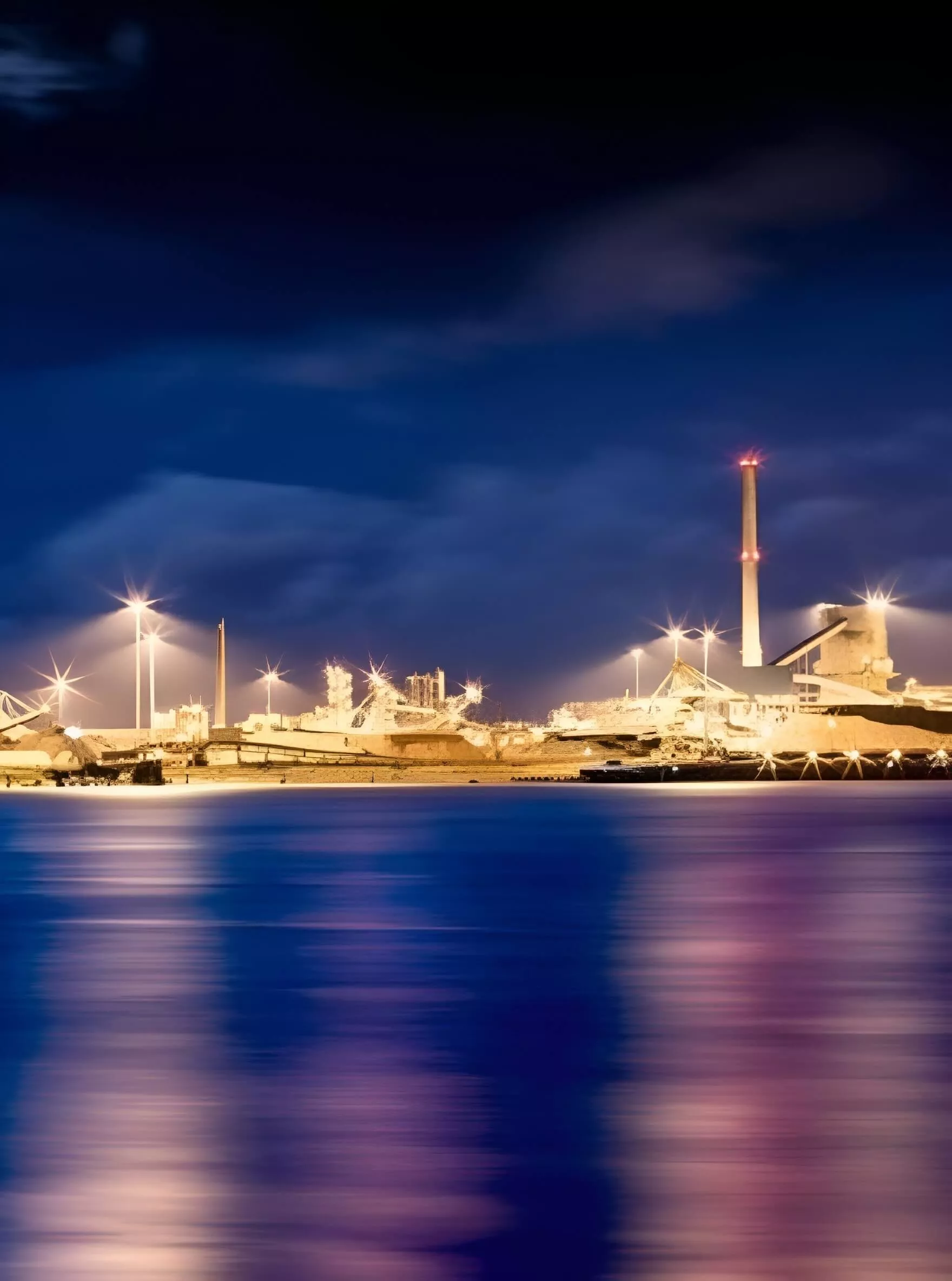
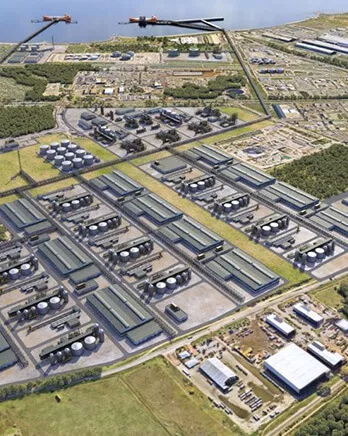
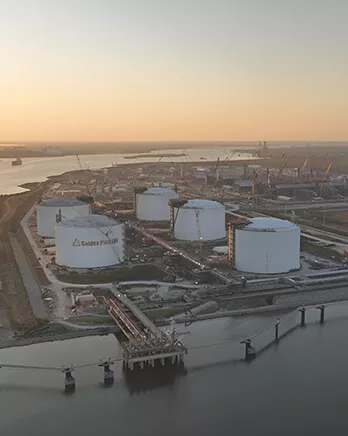

With projects ranging from demonstration to commercial-scale water electrolysis and over 200 steam methane reformer projects, McDermott’s integrated approach enables optimization from concept to completion.
Our expertise and partnerships enable us to offer alternative methane reforming technologies and find fit-for-purpose solutions. McDermott’s expertise is further boosted by a long history in CCUS and knowledge of CO2 compression and injection.
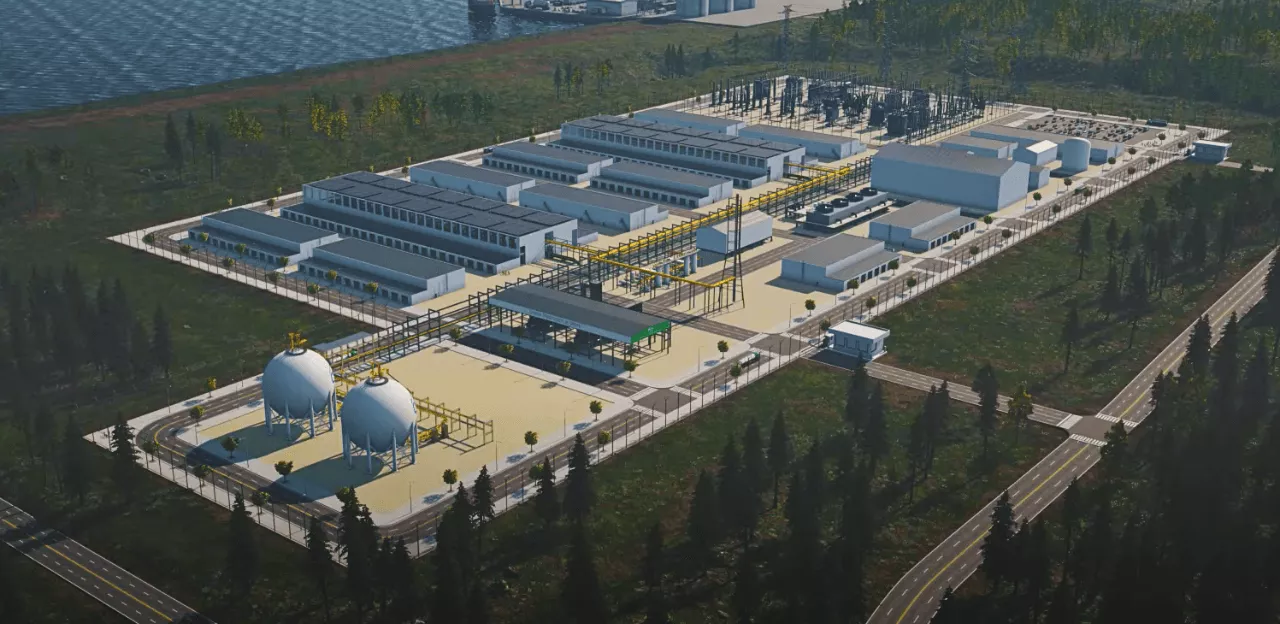
300 hydrogen projects executed across multiple industries
Experience across the hydrogen value chain in generation and derivatives.
Standardized modular solutions for hydrogen and ammonia production
Partnerships with key technology providers, including electrolysis, methane reforming, ammonia synthesis and carbon capture
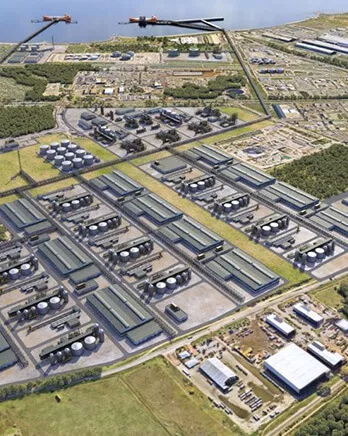
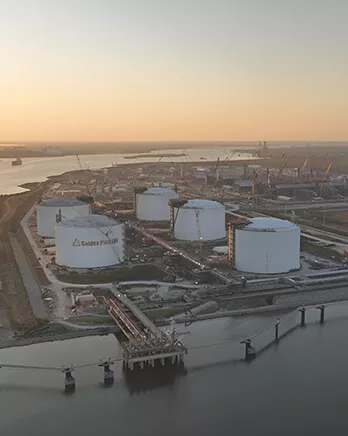
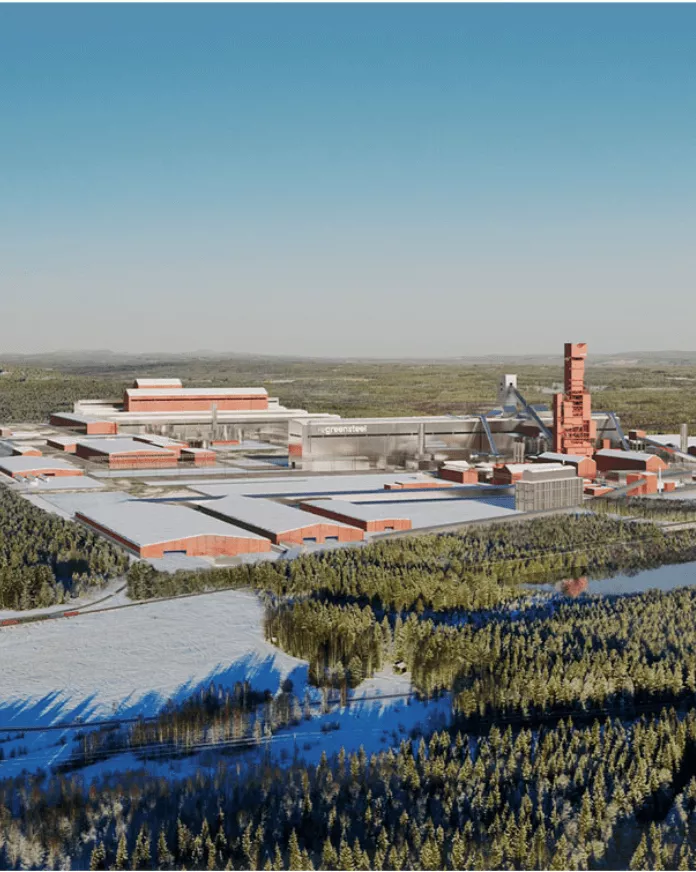
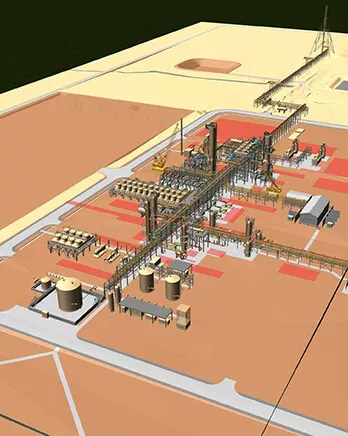
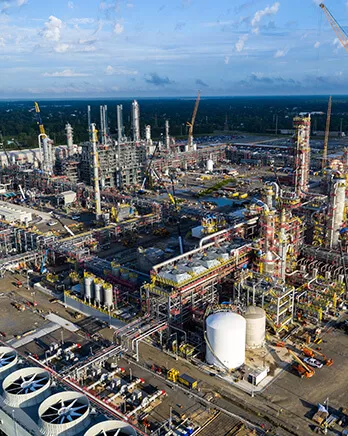
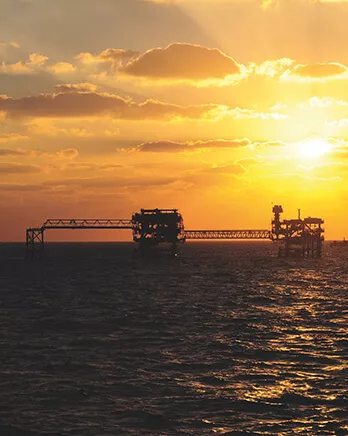
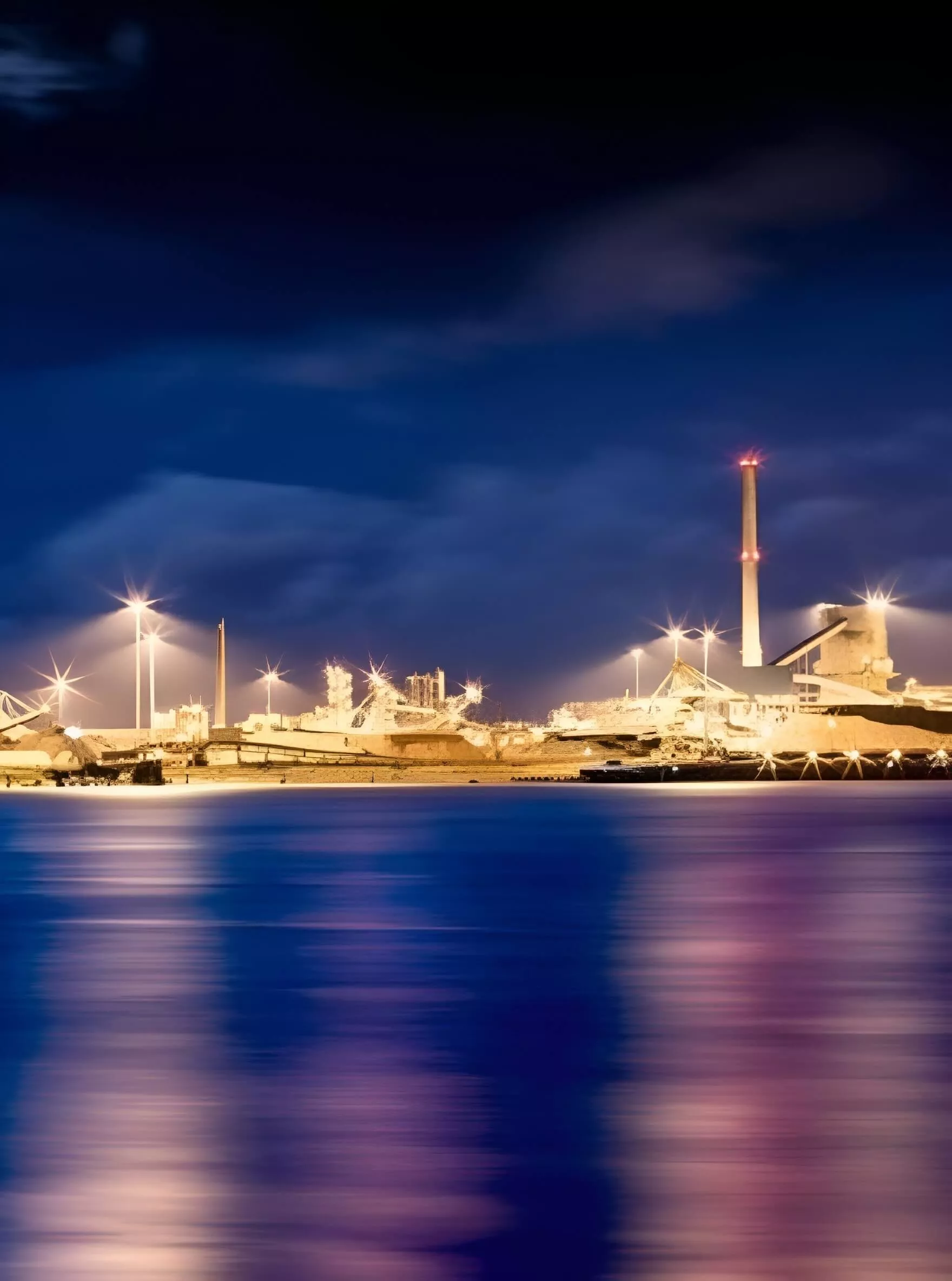
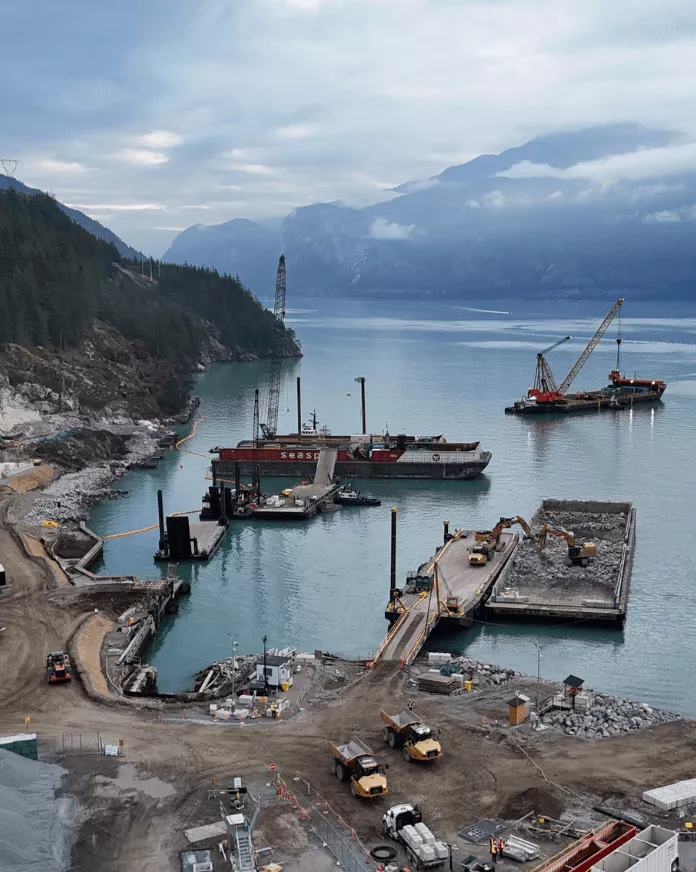
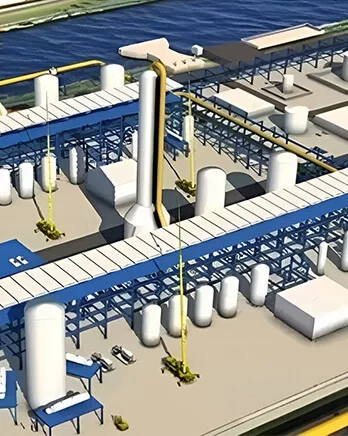

Through our in-house expertise and capabilities, and relationships with the industry’s top technology providers, combined with our proven engineering, procurement, fabrication, and construction services, we deliver full-scope product solutions and process technologies. We design and build everything from process units and plants to ambient temperature and cryogenic storage systems, and import/export terminals. We have provided specialty engineering, procurement, fabrication and construction services to the refining, chemical and petrochemical industry for more than 80 years.
McDermott provides comprehensive solutions for olefins, glycols, polymers and specialty chemicals facilities, integrated petrochemical complexes, clean fuels production, sustainable aviation fuels, heavy oil processing and crude-to-chemicals, individual refinery process units and related ancillary facilities solutions. Together, we’re preparing the industry for the energy transition and maximizing the value of current and future assets.
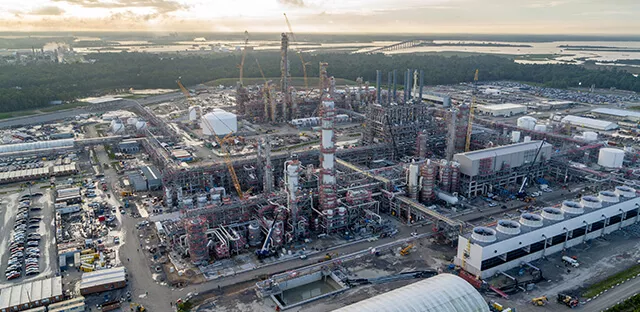
Wide breadth of process technology licensor experience
Full project lifecycle capabilities from licensor selection through front-end design and commissioning
Global execution centers
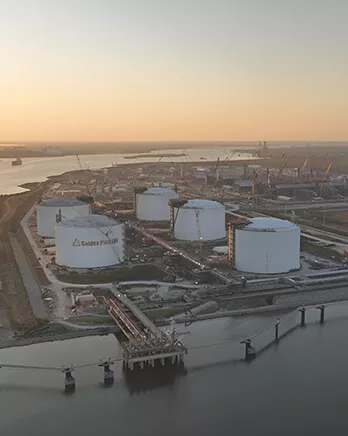
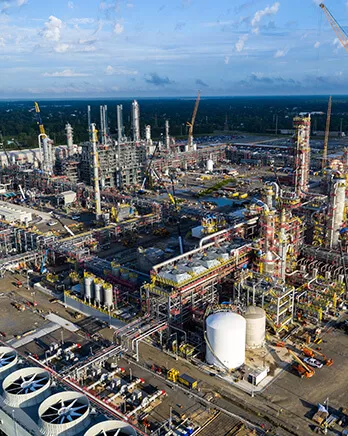
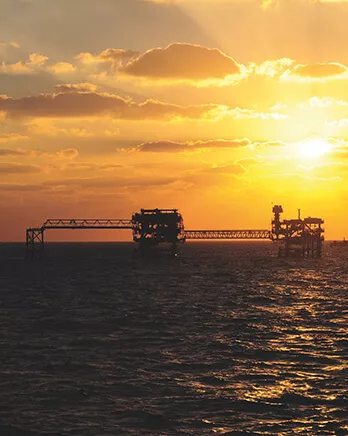
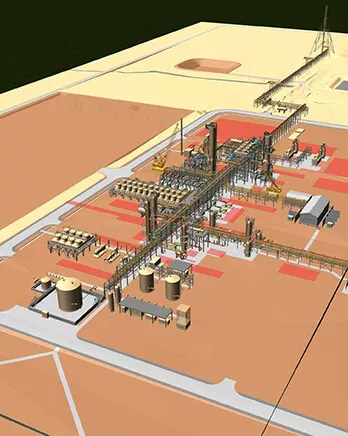
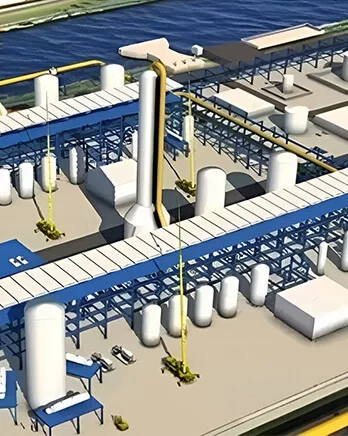
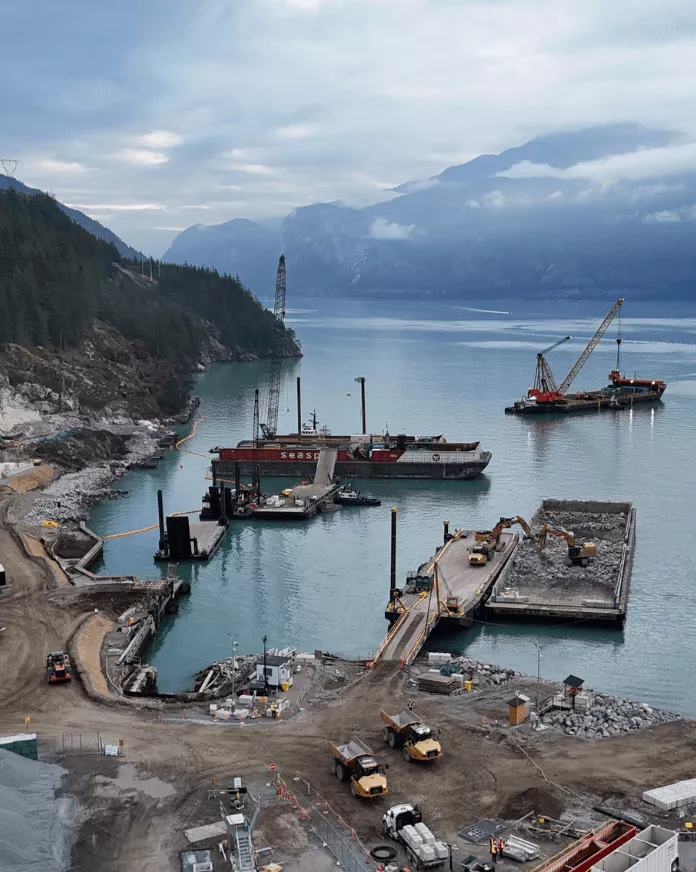
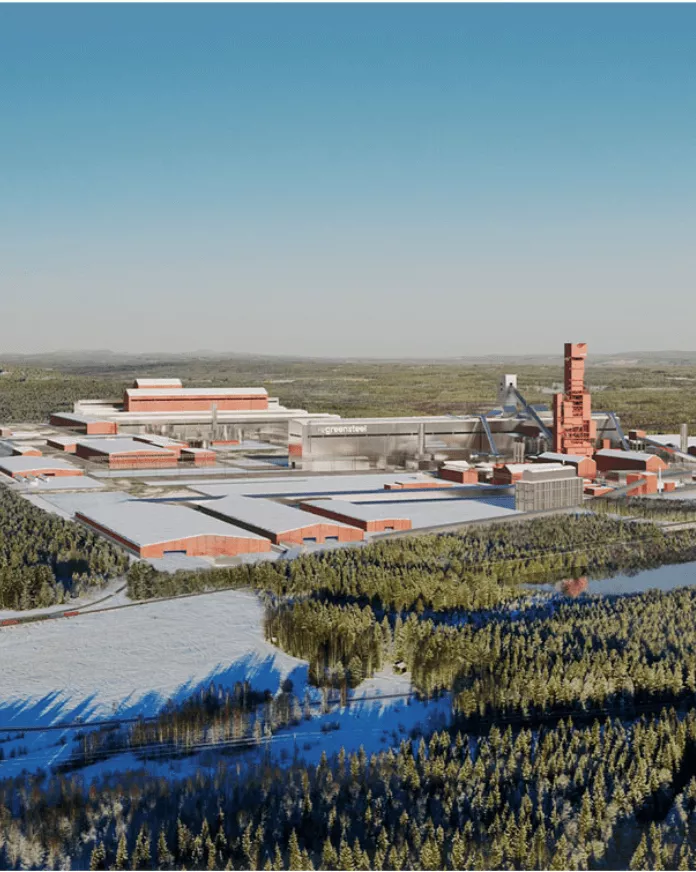

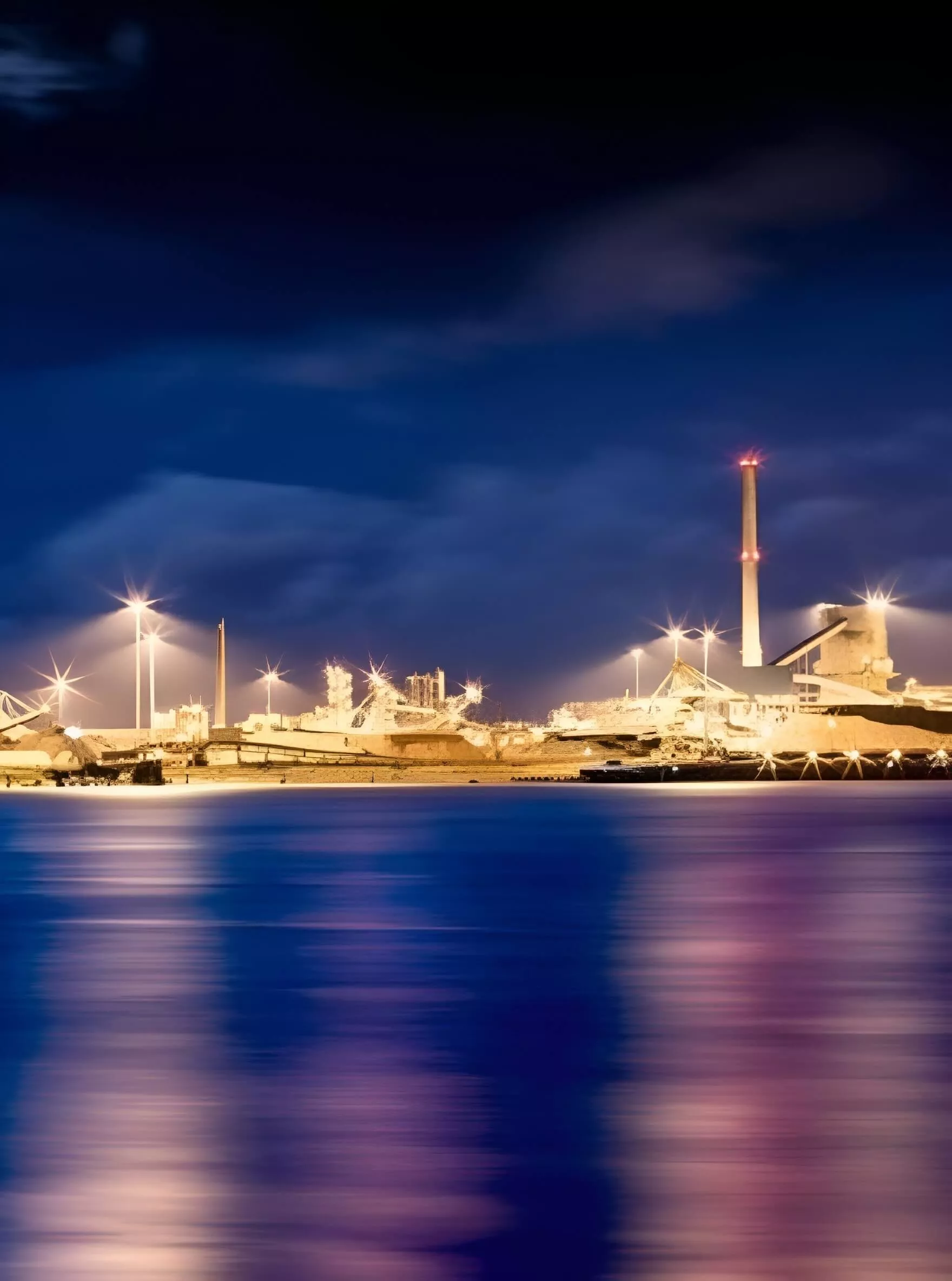
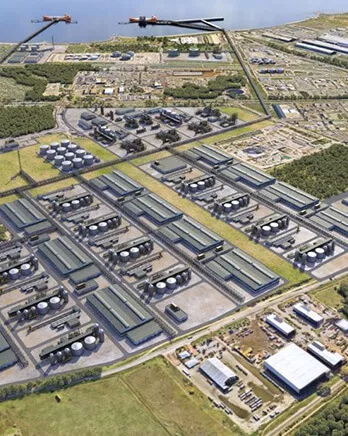
Throughout our more than 60 years serving the LNG industry, we have designed and built nearly every type of LNG project. McDermott is one of the few contractors that can perform the entire scope of work, executing and delivering the most complex projects successfully, safely and on time.
- Liquefaction plants
- Regasification terminals
- Peak shaving facilities
- Storage tanks
- FLNG topsides
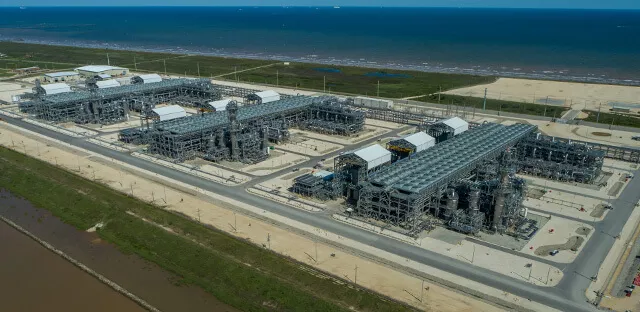
Modularization
E-drive
Net Zero LNG
Full lifecycle from concept to handover
Over 60 years’ experience
Storage solutions
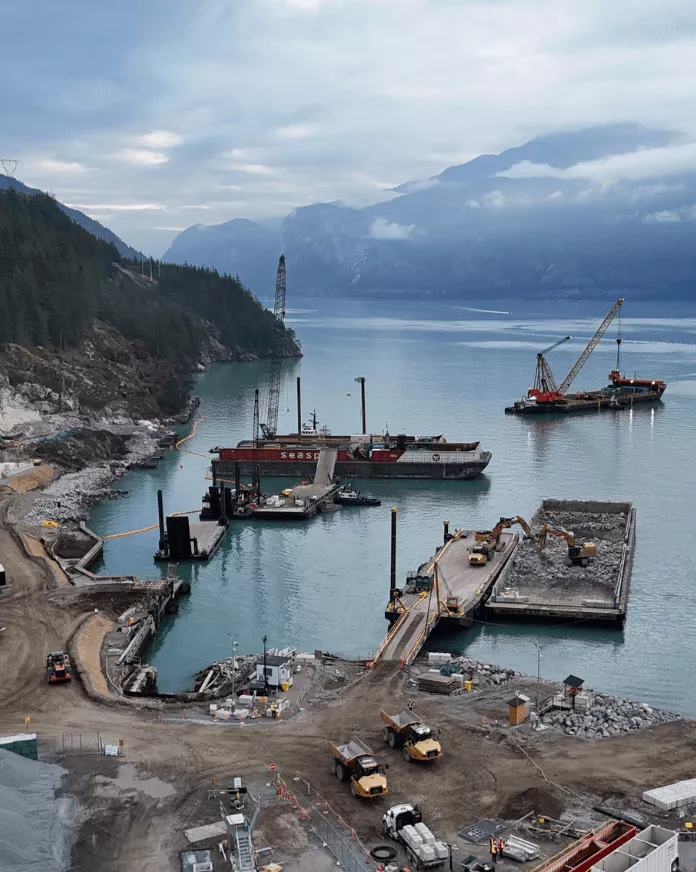
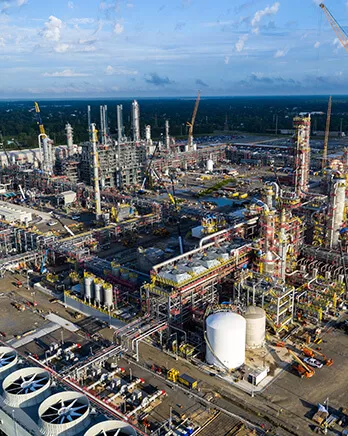
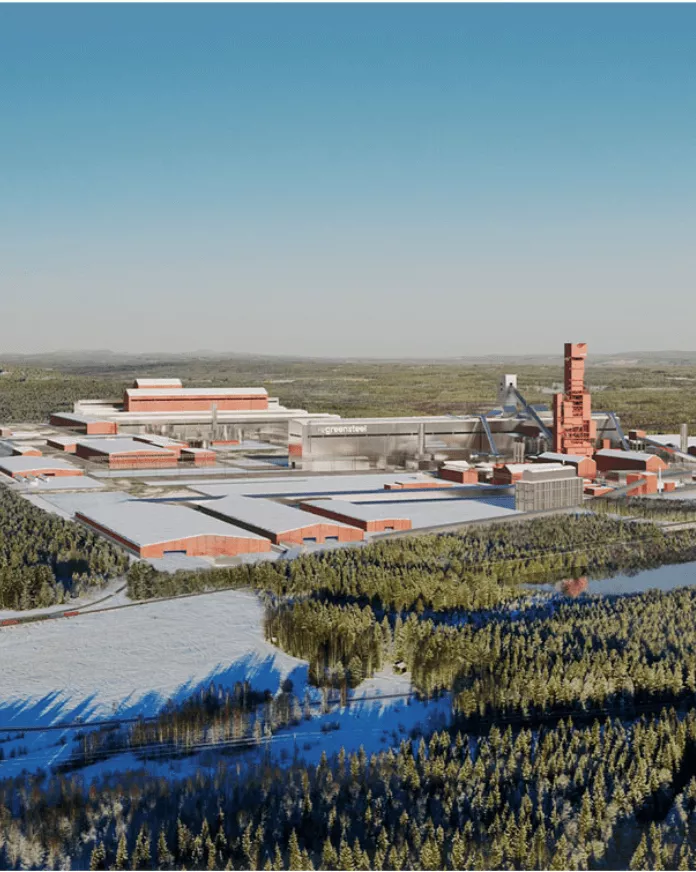
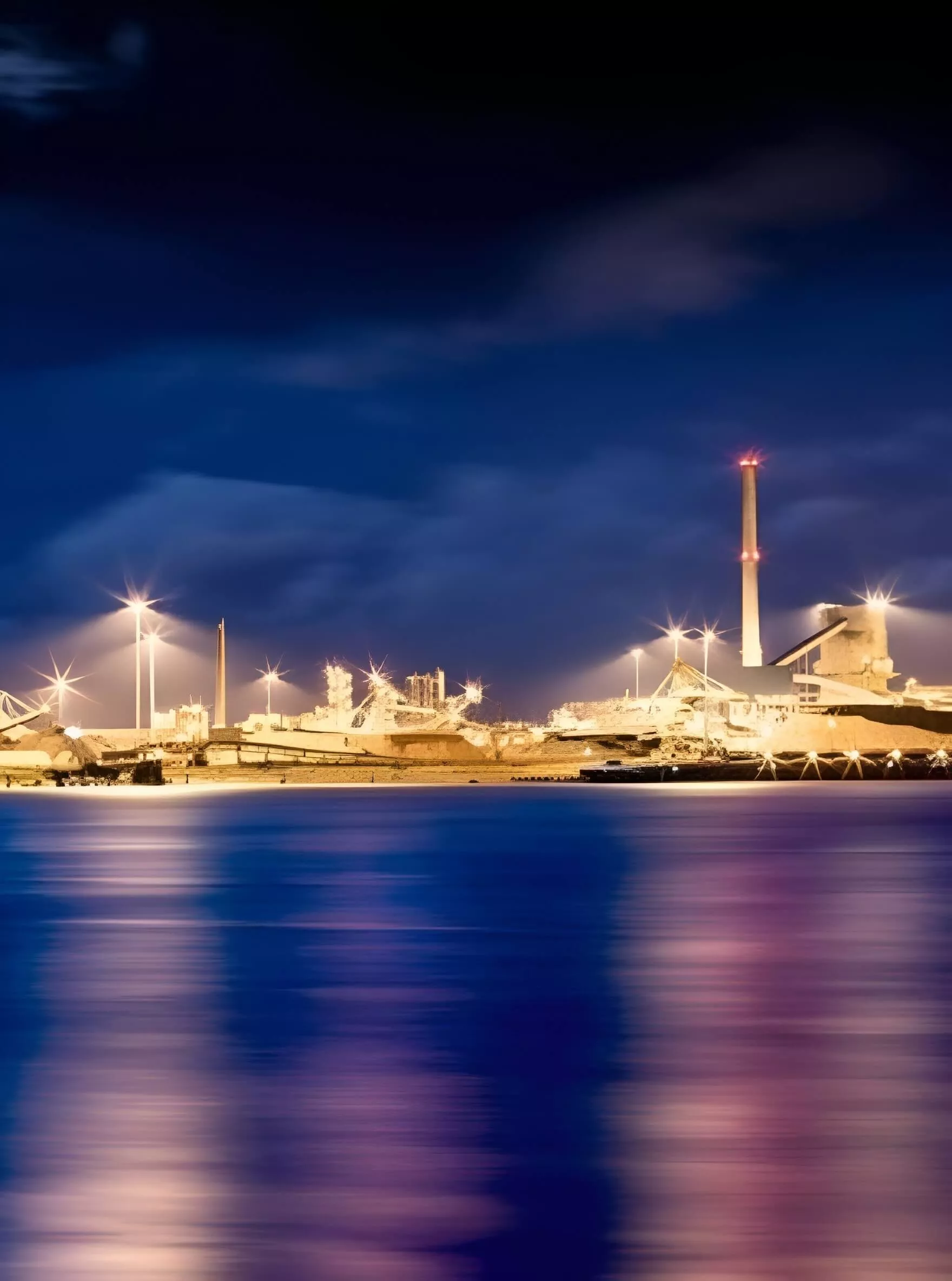
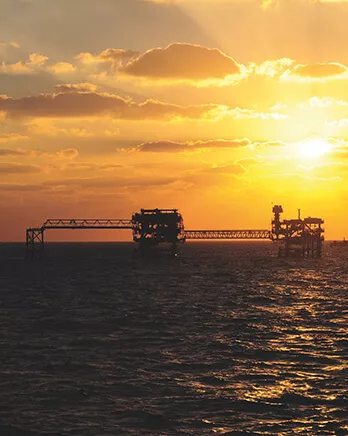
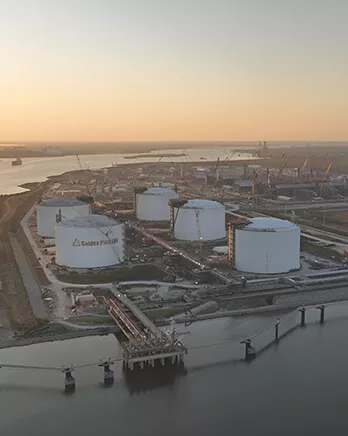
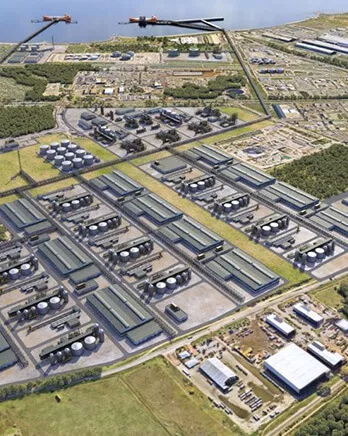
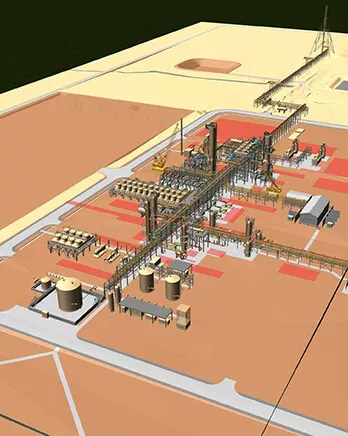

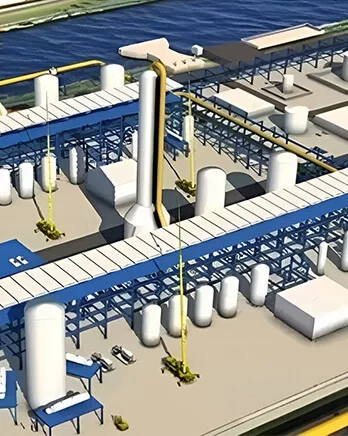
Global Footprint



